Case Histories
Downloads
Southern Wine and Spirits
Industrial
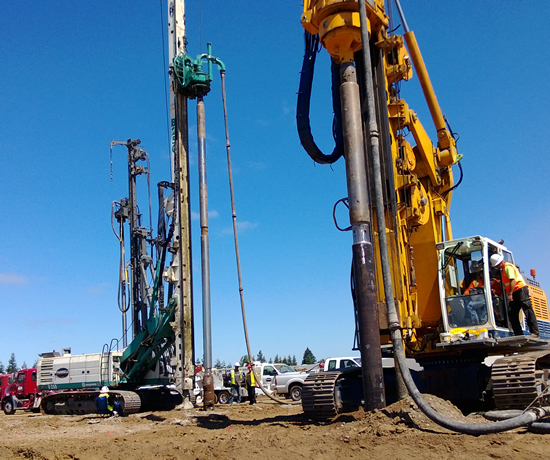
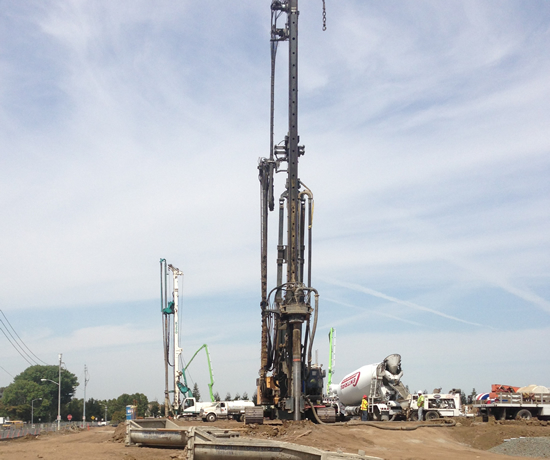
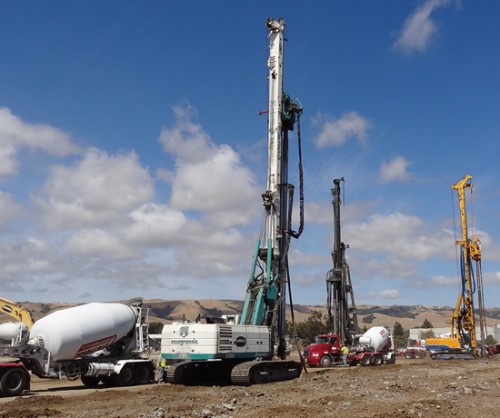
Foundation System
Geologic Hazard(s)

Soft/Loose Soil

Liquefaction

Contaminated Soil
Location
Union City, CA
Owner
Southern Wine and Spirits
Geotechnical Engineer
Structural Engineer
General Contractor
Project Summary
Southern Wine & Spirits expanded their distribution warehouse with a 300,000 square foot, heavily loaded, robotic inventory control system at their site in Union City. The site rests over compressible clay and liquefiable sand layers to depths of 40 feet. Cornerstone Earth Group recommended ground improvement for the project to control static settlements and improve the liquefiable layers to reduce seismic settlement. After a design-build competition, Whiting-Turning and the project team selected Farrell Design-Build’s proposed ground improvement solution using Drill Displacement Column™ (DDC).
With three rig/crews, Farrell installed over 2,000 DDCs to depths of 40 feet in just 40 days. Cornerstone Earth Group provided full-time quality assurance observation during the DDC load testing and installation operations. DDCs were utilized for settlement control of the new foundation loads and the mat-slab in the robotic inventory control area of the warehouse. The DDCs improved the weak, compressible soil and increased the density of the loose sand at depth. The DDCs also increased the allowable bearing capacity at the spread footings and at the robotic storage rack area. The strict settlement criteria in the robotic mat required less than 1/4 inch differential settlement in 50 feet for the 1,200 psf floor load.
Farrell’s engineers worked with BTI’s structural engineer on the very important mat-slab in the robotic area to optimize DDC layout, mat thickness, and concrete reinforcement. Farrell used RISA 3D finite element software to assist BTI’s design staff, which lead to a considerable cost savings for the project by reducing the mat from 18 inches to 14 inches thick.
Farrell started the project with 2 rig/crews, then increased to 3 rig/crews to accelerate the schedule at Whiting-Turner’s request. Farrell coordinated with the project team and began DDC installation early, while the existing building was still being demolished, to help the project launch an earlier start time. This innovative design-build solution provided by Farrell saved the project money all while delivering a robust, reliable, and strong ground improvement support system.
The project is also located in the ground water protection region of Alameda County Water District. Because of Farrell’s success working in this sensitive ground water region with DDC, we were able to develop a workplan for ACWD to approve the project and protect the precious ground water recharge program, helping another project Go Vertical with Confidence®.