Case Histories
Downloads
The A.J. at the Railyards
Commercial/Mixed Use
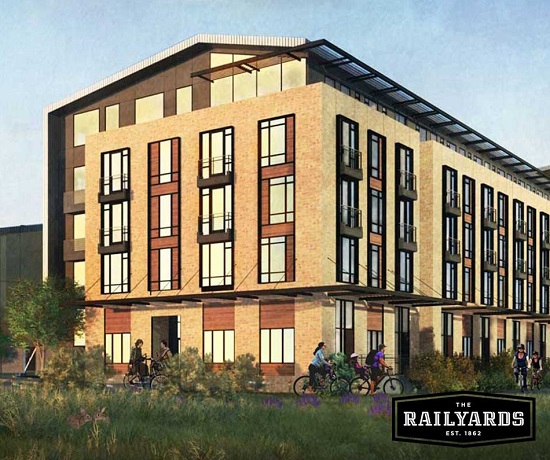
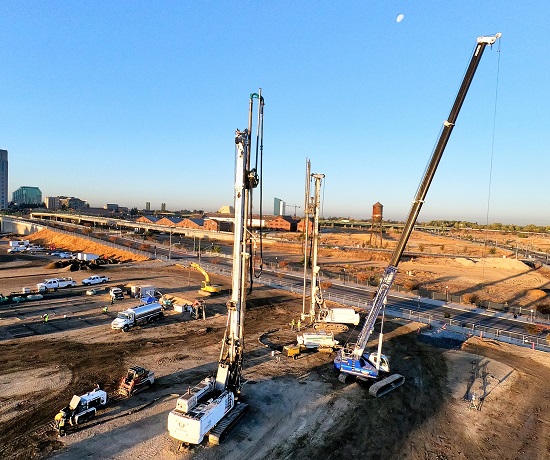
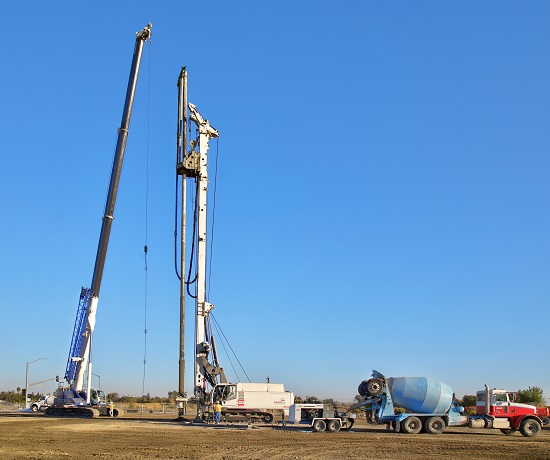
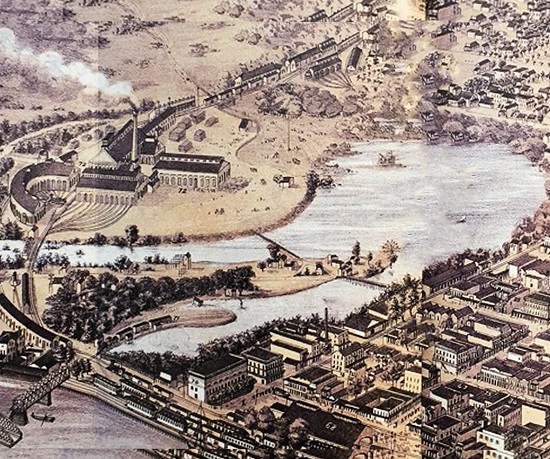
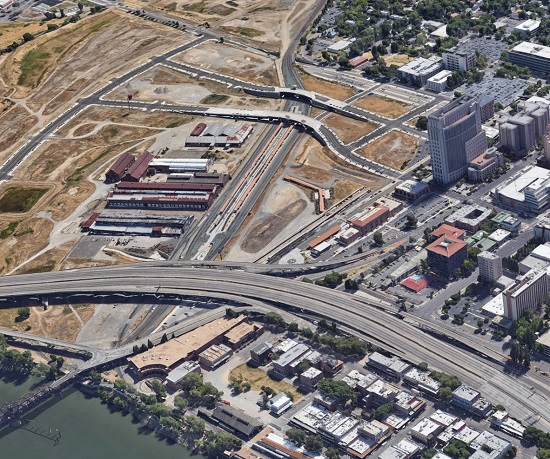
Foundation System
Geologic Hazard(s)

Soft/Loose Soil

Liquefaction
Location
Sacramento, CA
Owner
Downtown Railyard Venture
Geotechnical Engineer
Structural Engineer
General Contractor
The historic Sacramento Railyards is initially sprouting up with The A.J. The 2.9 acre residential project is taking root within the historic Sacramento Railyards, home to the largest industrial railroad facility west of the Mississippi River since the 1,800s and the primary departure station for the First Transcontinental Railroad. The project is named in honor of A.J. Stevens, Sacramento Railyard’s “Father of Innovation.”
The 6-story structure will offer 345 residential units, 69 of which will be affordable housing units, above ground-floor retail spaces. Residents of this Build it® Green complex (Gold standard for energy efficiency), will enjoy a dedicated parking structure, fitness center, pool, spa, dog wash, and a rooftop sky lounge with outdoor grills and fire tables. Farrell was selected by LDK Development and Brown Construction after two years of feasibility studies and multiple deep foundation and ground improvement cost studies.
During the Geotechnical Investigation, Sierra Geotechnical identified 5-feet of undocumented fill consisting of sand with clay and silt, sandy lean clay, and sandy lean clay with gravel. Beneath the fill, borings encountered young alluvial fan deposits consisting of interbedded layers of loose to medium dense sand and silty sand and soft to stiff silt and clayey silt extending to a depth of 68-feet. Very dense sand, gravel, and cobbles were observed below 70 feet. Groundwater was encountered at 20 feet, but historic data for the Railyards shows the groundwater table can be within 10 feet of the ground surface during winter months. Soil at the site is highly liquefiable under the design earthquake, with estimated seismic settlement approaching 4 to 6 inches. In addition to the Sacramento River on the west and the American River on the north, China Lake (also known as Sutter Lake) once existed at the site of the Railyards. By the 1850’s homes occupied much of the southern and eastern shorelines of China Lake, where Downtown Sacramento lies today. In 1863, the Central Pacific Railroad began to hydraulically fill the lake with sand from the American River and by 1910, the lake was completely filled and occupied by the Transcontinental Railyard operations.
Due to the site’s soft/loose soil conditions and in order to reach a vertical settlement of less than 1-1/2-inches, Farrell recommended Type 2 reinforced, Drill Displacement Column™ (DDC) ground improvement as A.J.’s concrete mat foundation support solution. At the A.J., the Type 2 DDC are designed to resist downdrag forces related to liquefaction and to support the structural concrete mat. DDC strengths are enhanced by the pressure grout effect during construction. DDC increases bearing capacity, increases soil stiffness, reduces soil compressiblilty, increases soil resistance to liquefaction, and increases composite soil shear strength. DDC goes deep. With two piling rigs and two crews, Farrell installed over 770, 16-inch diameter, steel reinforced, Type 2 Drill Displacement Column™ ground improvement columns to depths of 79 feet in just 7 weeks.
The advantages and versatility of DDC ground improvement in soft and deep liquefiable soil, demonstrates Farrell Design-Build’s innovation, teamwork, and value to design-build reliable, strong, engineered, “composite ground,” for long term foundation support for the A.J. to Go Vertical with Confidence!®